Construction Purchase Orders (POs) are essential documents in the construction industry that facilitate the procurement process for materials, services, and equipment. By providing clear instructions and ensuring transparency, construction POs streamline operations and help manage costs effectively. In this comprehensive guide, we will delve into the various aspects of construction purchase orders, including their definition, importance, key elements, creation process, types, management, and legal implications.
Understanding Construction Purchase Orders
Construction projects involve numerous transactions and agreements between various parties. One crucial document that formalizes these agreements is the construction purchase order. A construction purchase order is a legally binding document that solidifies the agreement between a buyer, typically the project owner or contractor, and a seller, which can be a vendor or supplier.
At its core, a construction purchase order outlines the specifics of the purchase, including the items or services required, quantity, price, delivery schedule, and terms of payment. By providing a written record of the transaction, purchase orders safeguard the interests of both parties involved and ensure compliance with contractual obligations.
Construction purchase orders play a vital role in managing project costs, inventory control, budget tracking, and maintaining a transparent procurement process. They serve as a crucial tool to prevent unauthorized purchases and eliminate any ambiguity that may arise during the procurement process. Additionally, purchase orders facilitate accurate financial record-keeping, allowing for better cost analysis and control.
Enforcing the use of purchase orders within construction companies minimizes the risk of project delays, disputes, and unexpected expenses. By clearly defining the terms and conditions of the purchase, both the buyer and seller can avoid misunderstandings and potential conflicts. This, in turn, contributes to smoother project execution and successful completion.
Sample Purchase Order for Construction Company Example
To get a more profound understandin on how purchase order sample for constcruion company looks like, take a look at the example below.
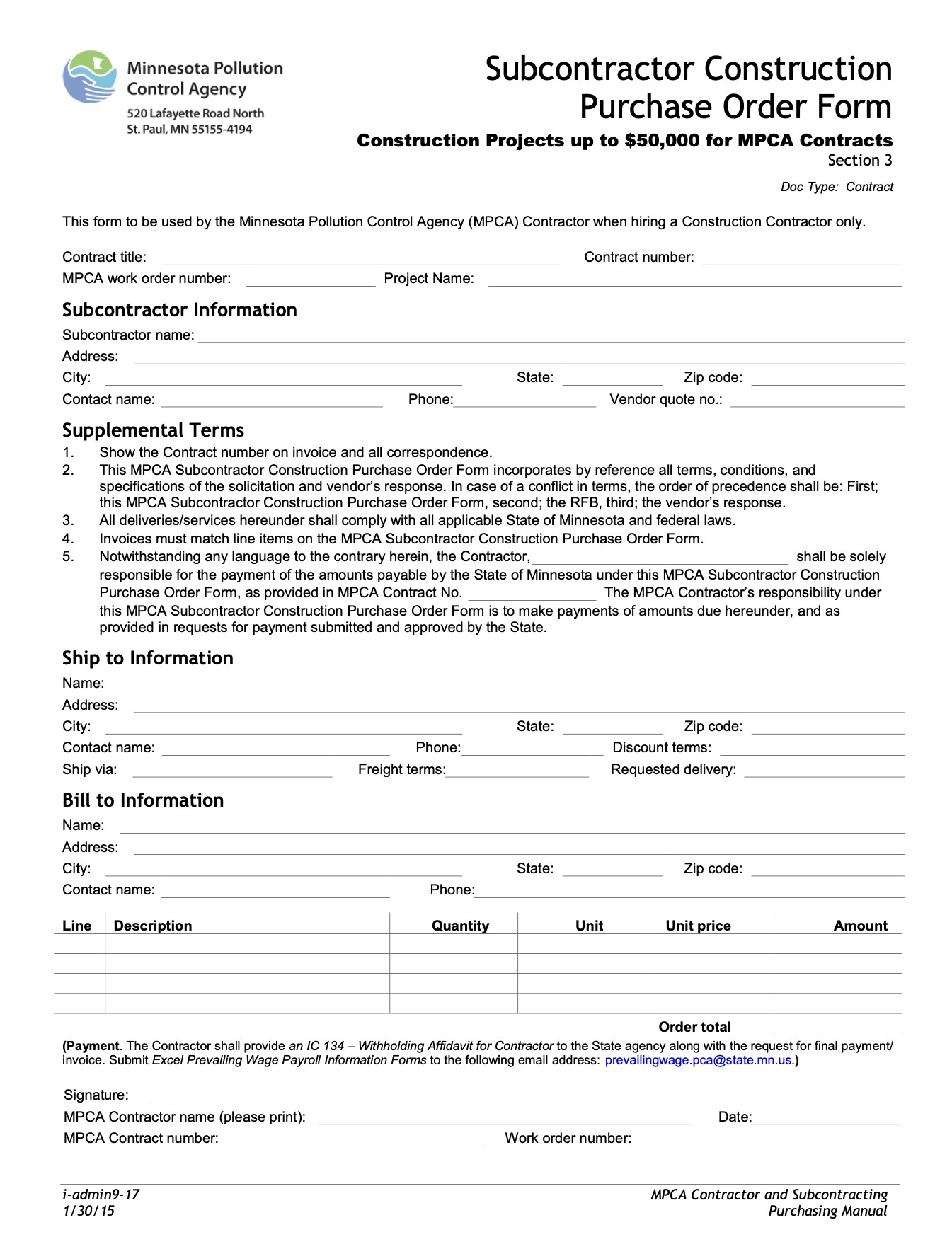
This example of a construction company PO template illustrates a straightforward construction purchase order, including necessary details such as item descriptions, quantities, prices, and payment terms.
Key Elements of a Construction Purchase Order
A well-structured construction purchase order typically contains several key elements that ensure clarity and accuracy:
- Header: The header section includes the company name, address, contact information, and a unique purchase order number. This information allows for easy identification and tracking of the purchase order throughout the project.
- Vendor Information: This section provides details about the supplier, including their name, address, and contact information. Having accurate vendor information is crucial for effective communication and coordination.
- Item Description: The item description clearly specifies the materials, equipment, or services required. It may also include any applicable specifications or standards that the items must meet. This ensures that the buyer receives the exact items they need for the project.
- Quantity: The quantity section indicates the number or amount of the items needed. This information helps the seller understand the scale of the order and ensures accurate fulfillment.
- Unit Price: The unit price states the cost per unit of the item. Multiplying the unit price by the quantity allows for the calculation of the total amount. This helps both parties understand the financial implications of the purchase.
- Total Amount: The total amount displays the overall cost of the purchase order, including any applicable taxes and additional charges. This information is crucial for budgeting and financial planning.
- Delivery Date: The delivery date section specifies the expected delivery or completion date. This allows the buyer to plan their project timeline accordingly and ensures timely delivery of the items or services.
- Terms of Payment: The terms of payment outline the payment method, due date, and any other relevant payment conditions. Clear payment terms help avoid payment delays and disputes.
- Terms and Conditions: The terms and conditions section includes any additional terms, warranties, or special instructions related to the purchase. This ensures that both parties are aware of any specific requirements or conditions that may apply.
By including these key elements in a construction purchase order, both the buyer and seller can establish a clear understanding of the transaction, mitigate risks, and ensure a smoother procurement process.
The Process of Creating Construction Purchase Orders
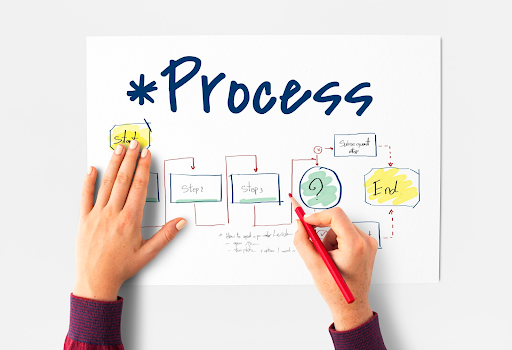
Creating construction purchase orders involves a series of steps that ensure a smooth procurement process and maintain financial control. Let's dive deeper into each stage to understand the intricacies involved.
Preparing for the Purchase Order
Before diving into the creation of a construction purchase order, it is crucial to gather all relevant information and ensure alignment with the project's procurement plan. This involves a comprehensive assessment of the procurement needs, considering factors such as quantity, quality, and timeline requirements.
Once the procurement needs are identified, construction professionals must obtain quotes or proposals from potential suppliers. This step allows for a thorough evaluation of different vendors, considering factors such as price, quality, and reliability. It is essential to verify the credentials and track record of potential suppliers to ensure they can meet the project's requirements.
Writing the Purchase Order
With the procurement requirements defined, it's time to draft the purchase order. Using a standardized template helps maintain consistency and ensures that all necessary information is included. The purchase order must be clear, concise, and unambiguous, leaving no room for misinterpretation.
It is crucial to include key elements in the purchase order, such as the vendor's name, contact information, item descriptions, quantities, prices, delivery dates, and payment terms. Providing a detailed and accurate description of the purchase helps avoid confusion and ensures that both parties are on the same page.
Approving and Issuing the Purchase Order
Before sending out the purchase order, obtaining the necessary approvals is essential. Depending on the construction company's hierarchy and protocols, the purchase order may require approval from various stakeholders, such as project managers, procurement managers, or executives.
Ensuring that the purchase order aligns with the approved budget and procurement plan helps maintain financial control and prevents unauthorized purchases. This step also allows for a final review of the purchase order, ensuring that all details are accurate and in line with the project's objectives.
Once all approvals are obtained, the purchase order can be issued to the selected vendor or supplier. Sending the purchase order via a secure and traceable method, such as email or a digital procurement platform, helps track communication and reduces the risk of misplacement or delays.
Types of Construction Purchase Orders
When it comes to construction projects, there are various types of purchase orders that are commonly used. These purchase orders serve different purposes and are designed to meet the specific needs of the project. Let's take a closer look at three types of construction purchase orders.
Standard Purchase Orders
A standard purchase order is the most common type used in construction projects. It is issued for one-time purchases and for items or services not covered by existing supply agreements. Standard purchase orders specify the quantity, price, and delivery details for the specific purchase, following the standard procurement process.
For example, let's say a construction company needs to purchase a specific type of construction material for a project. They would issue a standard purchase order to the vendor, specifying the quantity of the material required, the agreed-upon price, and the expected delivery date. This type of purchase order ensures that the procurement process is streamlined and that all parties involved are clear on the details of the purchase.
Planned Purchase Orders
A planned purchase order is a pre-approved document that outlines future procurement needs. It is used when the quantity, frequency, or timing of the purchases is predictable, allowing for efficient planning and budgeting. Planned purchase orders provide vendors with advanced notice, ensuring a smooth supply chain and minimizing lead time for critical items.
Let's say a construction company has a project that requires a significant amount of construction materials over a period of several months. In this case, they may issue a planned purchase order to the vendor, specifying the estimated quantities of materials needed each month. This type of purchase order helps the construction company and the vendor plan their resources effectively and ensures a steady supply of materials throughout the project.
Blanket Purchase Orders
Blanket purchase orders are used when a construction company has ongoing or recurring procurement requirements with a specific vendor. They establish a long-term agreement that covers multiple purchases within a defined period, typically one year. Blanket purchase orders provide flexibility and simplify the procurement process for frequently acquired items or services.
For example, a construction company may have an agreement with a specific equipment rental company to provide various types of machinery throughout the year. Instead of issuing separate purchase orders for each rental, the construction company can establish a blanket purchase order with the vendor. This allows them to request equipment rentals as needed, within the agreed-upon terms and conditions, without the need for individual purchase orders for each transaction.
Managing Construction Purchase Orders
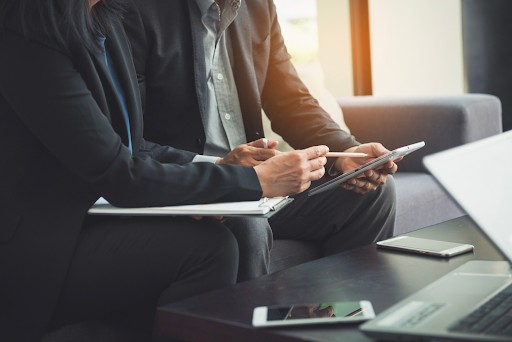
Tracking and Updating Purchase Orders
Efficient management of construction purchase orders involves diligent tracking and regular updates. Maintaining a centralized system, such as a project management system or enterprise resource planning (ERP) system, helps consolidate purchase order records, track delivery schedules, and monitor payment status. Regular communication with vendors and internal stakeholders ensures that any changes, delays, or discrepancies are promptly addressed.
Resolving Purchase Order Discrepancies
Occasionally, discrepancies or issues may arise regarding a construction purchase order. It is essential to resolve these discrepancies promptly to minimize disruptions and prevent potential cost overruns. Open and transparent communication with the vendor is crucial to understand the root cause and find mutually agreeable solutions. Resolving purchase order discrepancies may involve renegotiating terms, requesting replacements or refunds, or initiating dispute resolution procedures as per the contract.
Legal Aspects of Construction Purchase Orders
Contractual Obligations and Rights
Construction purchase orders form part of the contractual obligations between the buyer and the seller. They establish the obligations and rights of both parties and provide a legal framework for the procurement process. It is crucial to carefully review and ensure compliance with the terms and conditions specified in the purchase order, as well as any relevant laws or regulations governing the construction industry.
Dispute Resolution and Litigation
In the unfortunate event of a dispute or non-performance related to a construction purchase order, having clear dispute resolution mechanisms outlined in the contract becomes vital. Disputes may arise due to quality issues, delivery delays, payment disputes, or other conflicts. By specifying the preferred method of dispute resolution, such as mediation or arbitration, the parties can expedite the resolution process and avoid costly litigation.
In conclusion, construction purchase orders are indispensable tools for effective procurement management in the construction industry. By understanding their definition, importance, key elements, creation process, types, management, and legal implications, construction professionals can optimize their procurement practices, minimize risks, and maintain project success.