Understanding Procurement in Construction
Procurement in construction refers to the process of acquiring goods, services, or works for a construction project. It involves the selection of suppliers, negotiating contracts, and managing the entire supply chain to ensure the timely delivery of resources and materials.
The procurement method chosen for a construction project can significantly impact its overall success, as it determines how the project is organized, how risks are allocated, and how costs are managed. Therefore, it is crucial for construction professionals to have a deep understanding of the different procurement methods available.
Definition of Procurement in Construction
In the context of construction, procurement refers to the purchase of materials, equipment, and services necessary for the completion of a construction project. This includes everything from raw materials like cement and steel to specialized machinery and skilled labor.
Procurement also involves the establishment of contracts between the client and the various suppliers and contractors involved in the project. These contracts define the terms and conditions of the procurement process, such as the scope of work, delivery schedules, and payment terms.
When it comes to procurement in construction, it is essential to consider the specific needs of the project. For example, if the project requires a high level of customization, the procurement process may involve sourcing specialized materials or engaging with suppliers who can provide customized solutions. On the other hand, for projects with standardized requirements, the procurement process may focus more on finding suppliers who can provide cost-effective and readily available materials.
The procurement process in construction often involves multiple stakeholders, including architects, engineers, contractors, and subcontractors. Each stakeholder may have different requirements and preferences, which need to be considered during the procurement process. Effective communication and collaboration among all parties are crucial to ensure that the procurement process meets everyone's needs and aligns with the project's objectives.
Importance of Procurement in Construction
Efficient procurement is crucial for the success of construction projects. It ensures that the right resources are available at the right time and place, minimizing delays and cost overruns. Additionally, effective procurement practices can help optimize project costs, improve quality control, and mitigate risks.
One of the key benefits of strategic procurement in construction is the ability to leverage economies of scale. By consolidating the purchasing power of multiple projects or by entering into long-term agreements with suppliers, construction professionals can negotiate better prices and terms, resulting in cost savings for the project.
Moreover, procurement plays a vital role in ensuring the quality of materials and services used in construction projects. Through rigorous supplier selection processes, construction professionals can identify and engage with suppliers who have a proven track record of delivering high-quality products and services. This helps to minimize the risk of using substandard materials or working with unreliable contractors, which can lead to costly rework and project delays.
By carefully selecting suppliers and contractors, construction professionals can establish reliable partnerships and ensure that the project is executed smoothly. Procurement also plays a vital role in promoting sustainability within the construction industry by encouraging the use of environmentally friendly materials and practices. For instance, construction projects can prioritize the procurement of materials with low carbon footprints or engage with suppliers who follow sustainable manufacturing processes.
Traditional Procurement Method
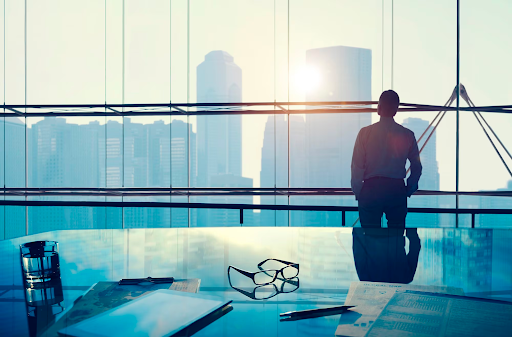
The traditional procurement method, also known as the design-bid-build method, is one of the most commonly used approaches in the construction industry. It follows a sequential process, where the design phase precedes the procurement of contractors and suppliers.
Overview of Traditional Procurement
In the traditional procurement method, the client first hires an architect or engineer to develop the project's design. This design phase involves detailed planning and consideration of various factors, such as functionality, aesthetics, and structural integrity. The architect or engineer works closely with the client to understand their requirements and translate them into a comprehensive design.
Once the design is finalized, the client invites competitive bids from contractors to carry out the construction work based on the design specifications. This bidding process ensures that multiple contractors have the opportunity to present their proposals and compete for the project. It also allows the client to evaluate different options and select the contractor that best meets their needs.
After reviewing the bids, the client selects the contractor with the most favorable terms and awards them the contract. This decision is based on factors such as price, experience, reputation, and proposed timeline. The contractor then procures the necessary materials, hires subcontractors if needed, and begins construction according to the agreed-upon schedule.
Pros and Cons of Traditional Procurement
Pros:
- Clear separation of design and construction responsibilities, reducing conflicts of interest. This separation allows each party to focus on their respective areas of expertise, leading to better outcomes.
- Allows for competitive bidding, potentially leading to lower costs. The bidding process encourages contractors to offer competitive prices, which can benefit the client.
- Well-established and familiar process for both clients and contractors. The traditional procurement method has been used for many years and is widely understood by industry professionals, making it easier to navigate.
- Provides a structured approach to project delivery, ensuring that each phase is completed before moving on to the next. This sequential process helps to maintain order and minimize confusion.
Cons:
- Design changes during construction can be expensive and time-consuming. Since the design phase is completed before the construction phase begins, any changes or modifications to the design may require additional time and resources.
- Minimal collaboration between the client, designer, and contractor during the design phase. The traditional procurement method does not emphasize collaboration between these parties, which can limit the opportunity for innovative ideas and integrated solutions.
- Potential for adversarial relationships between parties. The sequential nature of the traditional procurement method can create a sense of competition and adversarial relationships between the client, designer, and contractor, which may hinder effective communication and cooperation.
- Less flexibility in adapting to changing project requirements. Once the design is finalized and the construction phase begins, it can be challenging to accommodate changes or new ideas without significant disruptions to the project.
Despite its limitations, the traditional procurement method continues to be widely used in the construction industry due to its familiarity and established processes. However, alternative procurement methods, such as design-build and construction management, are gaining popularity for their collaborative and flexible approaches to project delivery.
Design and Build Procurement Method
The design and build procurement method, also known as the turnkey approach, offers a more streamlined and integrated process compared to traditional procurement. It involves the appointment of a single entity responsible for both the design and construction of the project.
Understanding Design and Build Procurement
In the design and build procurement method, the client contracts a design and build contractor directly. This contractor then takes on the responsibility of both the design and construction aspects of the project. The client provides a broad project brief, and the contractor develops a detailed design based on that brief.
This approach offers greater collaboration and efficiency as the design and construction teams work together from the beginning of the project. It allows for more flexibility and faster decision-making, reducing the time required for design revisions and change orders.
Advantages and Disadvantages of Design and Build Procurement
Advantages:
- Single point of responsibility, minimizing conflicts and improving coordination.
- Potential for faster project delivery due to early involvement of contractors.
- Greater flexibility in accommodating design changes during construction.
Disadvantages:
- Less transparency in the selection process compared to competitive bidding.
- Reliance on the contractor's design capabilities and expertise.
- Potential for cost overruns if design changes are frequent or poorly managed.
Management Contracting Procurement Method
The management contracting procurement method involves the appointment of a management contractor who oversees the entire construction process on behalf of the client. This method is typically used for large, complex projects that require specialist expertise.
Exploring Management Contracting Procurement
In the management contracting procurement method, the client appoints a management contractor early in the project. The management contractor's role is to manage the design and construction process, coordinating the various contractors and suppliers involved.
The management contractor acts as a facilitator, ensuring that the project progresses smoothly and according to the client's requirements. They are responsible for engaging and managing specialist sub-contractors, procuring materials, and overseeing the construction activities.
Strengths and Weaknesses of Management Contracting Procurement
Strengths:
- Early appointment of the management contractor allows for their input during the design phase.
- Greater potential for innovation and collaboration among contractors and suppliers.
- Procurement flexibility allows for better adaptation to project changes.
Weaknesses:
- Increased level of complexity and coordination required.
- Higher level of risk as costs and timeframes may be more difficult to control.
- Potential for conflicts between contractors and the management contractor.
Construction Management Approach in Procurement
The construction management approach involves appointing a construction manager who serves as a consultant to the client throughout the project lifecycle. The construction manager provides expertise and guidance, but the direct responsibility for design and construction lies with the client.
Understanding the Construction Management Approach
Under this approach, the construction manager is engaged from the earliest project stages, providing advice on design, construction feasibility, and tendering. They provide advice on design, construction feasibility, and tendering. The client retains control of the project and retains separate contracts with various contractors and suppliers.
The construction manager's role is to provide guidance, oversee the construction activities, and manage the various contractors on behalf of the client. Their expertise helps ensure that the project is delivered according to the client's specifications, schedule, and budget.
Pros and Cons of the Construction Management Approach
Benefits:
- Early involvement of the construction manager allows for their input during the design phase.
- Client retains control over the project and has direct relationships with contractors.
- Higher level of transparency and cost control throughout the project.
Drawbacks:
- Increased responsibility and decision-making burden on the client.
- Potential for conflicts or disputes between contractors and the construction manager.
- Requires a high level of collaboration and communication between all parties involved.
In conclusion, the procurement method chosen for a construction project in the UK is a critical decision. Each procurement method comes with its own set of advantages and disadvantages, and the choice should be based on the project's specific requirements, complexity, and the desired level of client involvement. By carefully evaluating the options and considering factors such as risk allocation, collaboration, and cost management, construction professionals can ensure the successful execution of construction projects in the UK.