The effectiveness of your procurement system is crucial for maximizing ROI. Ineffective procurement and unregulated purchasing have around a 30% impact on the company's bottom line, affecting potential savings and resulting in unnecessary costs.
Throughout this article, we will review the most common procurement mistakes to avoid to maximize ROI. So, let’s dive into it.
Importance of Avoiding Procurement Mistakes
Before diving further into the guide, let’s first understand the importance of avoiding procurement mistakes.
By avoiding mistakes in procurement:
- Reduces the risk of financial losses due to poor purchasing decisions.
- Ensures consistent supply chain operations without delays.
- Helps maintain strong supplier relationships and trust.
Most Common Procurement Mistakes
As far as we are clear on the importance of avoiding procurement mistakes, let’s overview the most common ones. In this section, we will cover mistakes such as:
- Inaccurate Material Information
- Lack of Negotiations
- Accidentally buying duplicate or unneeded items
- Employees ignoring or skipping the established purchasing process
- Rushed, last-minute purchases made in a panic
- Fraudulent purchases or suspicious transactions
- Poor supplier performance that causes delays or quality issues.
We will provide you with a comprehensive overview of the main causes and potential solutions to help you navigate modern-day procurement.
Inaccurate Material Information
The procurement team can accidentally order the wrong items when the materials' details are incorrect. Inaccuracies include inaccuracies such as specifications or type, color, quantity, and else. It often stems from poor documentation or unclear communication with suppliers.
The consequence of the mistake can be quite costly. For instance, if a construction company orders “steel rods” based on incorrect specs, they may get materials that don’t meet safety standards. This can lead to project delays and extra costs for replacing the items.
Lack of Negotiations
Another common mistake made in procurement is a lack of negotiations with the suppliers. Failing to negotiate can result in unfavorable contract terms and higher delivery costs. Also, it will result in missed opportunities for expense reduction and securing better delivery terms.
For instance, in the real world, if a retailer skips negotiations, they might end up paying much more than their competitors for the same products. This would lower their profit margins significantly.
Accidentally buying duplicate or unneeded items.
Due to a lack of proper management systems, some procurement teams order the same materials more than once. Or they can even purchase items that are not necessary due to poor inventory tracking.
In short, the potential consequences of duplicate purchases are:
- Leads to unnecessary financial expenses and ties up capital in unneeded stock.
- Increases storage and inventory management costs for excess materials.
- Causes potential waste if items become obsolete or unusable over time.
Employees ignore or skip the established purchasing process.
If the procurement policy is nonexistent or unenforceable, then employees might try to bypass it to place the orders without additional “complications.” This can lead to inconsistent purchasing, higher costs, and non-compliance with the company’s policies.
Rushed, last-minute purchases made in a panic
When companies leave procurement decisions to the last minute, they often pay a premium for expedited shipping or rush orders or settle for suboptimal materials. So, it is increasingly important to set clear procurement management policies in place to avoid such situations.
Fraudulent purchases or suspicious transactions
Fraudulent purchases are another procurement mistake that is a consequence of improper management. Fraud or unauthorized purchases occur if there is a lack of internal control and lack of oversight within the organization.
For instance, if a procurement officer makes fraudulent purchases from fake vendors, the company will lose money until the fraud is discovered.
Poor supplier performance that causes delays or quality issues
Selecting unreliable suppliers or failing to monitor supplier performance can result in delays, defective materials, or failure to meet contractual obligations. That is why it is highly advised to dedicate the right amount of resources and time to supplier sourcing and negotiations.
If a supplier delivers poor-quality materials consistently, the company may produce defective products, which leads to customer complaints and costly returns.
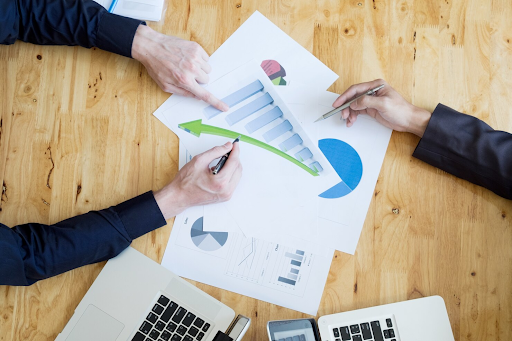
How to Avoid Procurement Mistakes?
Considering the consequences of procurement mistakes and their financial impact on the company's bottom line, a natural question arises - how can these mistakes be avoided? Well, you can implement no single solution to avoid every mistake, but there are c complex solutions.
To efficiently avoid procurement mistakes, you need to do the following:
- Implement the right technology
Use procurement software to automate purchasing processes, track spending, and ensure compliance with approved vendors and budgets.
- Establish clear purchasing protocols.
To minimize errors and confusion, set clear guidelines for employees to follow, including vendor approval, order procedures, and budget limits.
- Conduct regular training
Provide ongoing employee training on procurement policies and best practices to ensure everyone understands and follows the correct procedures.
Avoid Costly Mistakes and Improve Procurement Efficiency with Tradogram
If you are looking for the perfect software solution that will help you increase the efficiency of your procurement processes and avoid procurement mistakes, then you are in the right place. Tradogram is an all-in-one procurement management solution that will help you optimize and streamline the purchasing process.
Tradogram offers features such as multi-level management, supplier and inventory management tools, approval workflow customization, report builder, budgets, spend analysis, and robust analytics. Contact us to learn more about how Tradogram can help you avoid procurement mistakes and improve procurement efficiency.