TRUSTED BY MANY COMPANIES WORLDWIDE
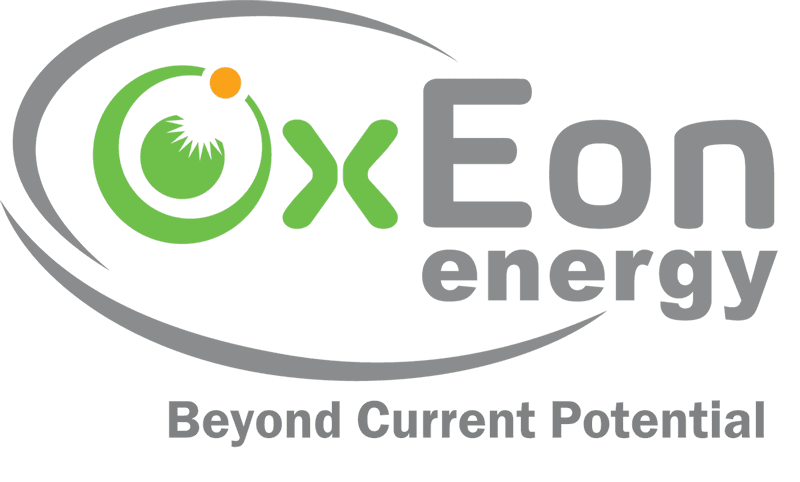
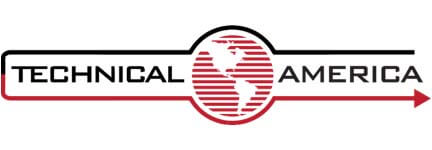
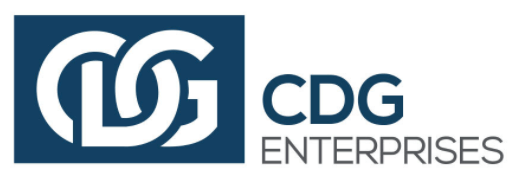
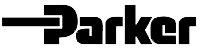
Meet Tradogram’s next-gen purchasing software for manufacturing. Adopt sustainable manufacturing processes, make better, data-driven decisions, and combat rising raw material costs with ease.
Meet Market Demands with Sustainable Procurement
Reduce purchase order processing time from days tominutes.
Enhance Supplier Collaboration for Smarter Purchasing
Manufacturing purchasing solutions slash costs by over 20% on average.
Go Digital & Ensure Compliance with Procurement Tools
Say goodbye to outdated, manual procurement processes and gain 100% spend visibility.
SEE TRADOGRAM IN ACTION
- Free Trial Account
- Free Live Demo
- Free Custom Quote
TRADOGRAM'S MANUFACTURING PROCUREMENT SOFTWARE DRIVING INDUSTRY TRANSFORMATION
As we ease further into Industry 4.0, manufacturing processes are changing, and procurement professionals must keep up with the times or fade into obscurity.
Build Stronger Supplier Networks for Sustainable Growth
Supplier management capabilities help you find sustainably sourced materials for the best prices.
Supplier evaluation scorecards ensure the suppliers you partner with are reliable and consistently meet performance expectations.
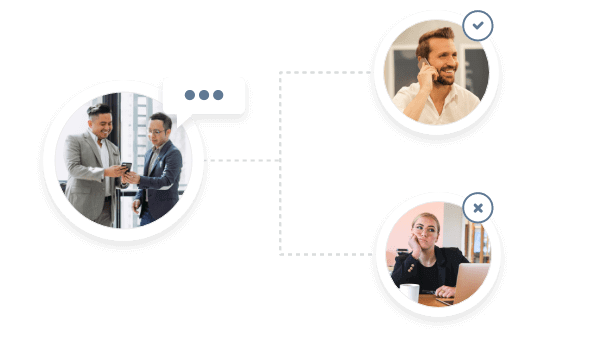
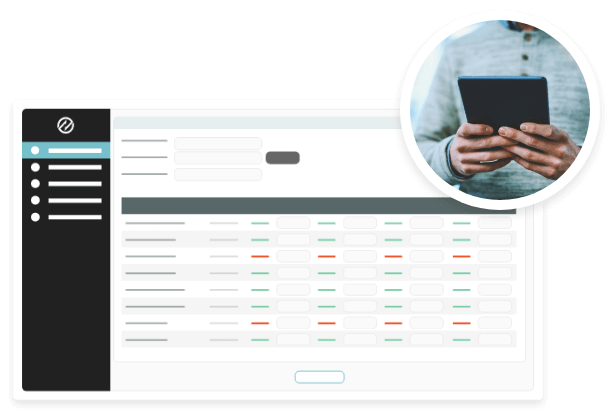
Ensure Stock Availability & Prevent Production Delays
Advanced inventory controls ensure a constant supply of critical supplies and equipment.
Standardized purchase order workflows eliminate the risk of dirty data by obligating system users to follow set processes and enter necessary data the right way.
Innovative Solutions to Rising Raw Material Costs
Spend analysis reporting tools let decision-makers see where the greatest ROI lays and avoid overspending when it’s not absolutely necessary.
Budget management features provide maximum purchasing transparency.
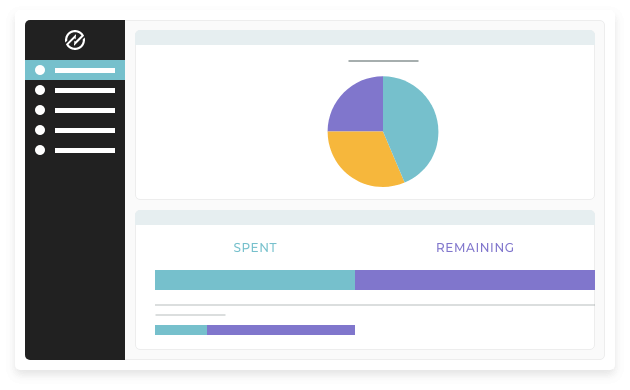